Coatings
Mass Balance Approach
A low-carbon, circular economy necessitates a transition to non-fossil raw materials derived from biomass or waste. The mass balance approach serves as an effective allocation scheme to facilitate this transition in a rapid, economical, scalable, and socially accepted way for a wide range of products.
Under the mass balance approach, BASF's Coatings division leverages both the biomass balance approach and ChemCycling® to significantly reduce CO2 emissions and conserve fossil resources, thereby contributing to a more sustainable future.
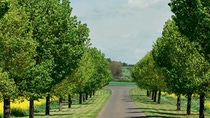
Biomass Balance (BMB) Approach
The biomass balance principle works similarly to green electricity, in which the electricity that comes from the socket is not necessarily generated from renewable sources, but a corresponding amount of renewable electricity is fed into the grid.
In the biomass balance approach, renewable resources such as bio-naphtha or biomethane derived from organic waste, crops or vegetable oils are used as feedstock in the very first steps of chemical production. The bio-based feedstock amount is then attributed to specific products sold by means of the certified method.
OEM Coatings: Jointly pioneering our industry
BMW Group has chosen to use BASF Coatings’ CathoGuard® 800 ReSource e-coat at its plants in Leipzig, Germany, and Rosslyn, South Africa, and the iGloss® matt ReSource clearcoat throughout Europe. The BMW Group has been the first carmaker to place its trust in more sustainable automotive OEM coatings certified according to BASF’s biomass balance approach.
Sustainability benefit
Using these more sustainable product versions for vehicle coatings enables CO2 avoidance of around 40% per coating layer; this will reduce the amount of CO2 emitted in the plants by more than 15,000 metric tons by 2030.
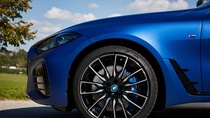
Reduction of CO2 emitted in plants by more than 15,000 metric tons by 2030
BASF Coatings launched the first biomass balance automotive coatings in China, providing more sustainable coating solutions without compromising on quality. The ColorBrite® Airspace Blue ReSource basecoat is certified by REDcert², adhering to the biomass balance approach.
Sustainability benefit
Basecoat product enables around 20% reduction in product carbon footprint. ColorBrite® ReSource adds a reduced carbon footprint without the need to alter the product’s formulation and performance.
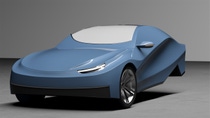
~20% reduction in product carbon footprint
BASF's Coatings division is gradually rolling out its eco-efficient refinish clearcoats and undercoats, manufactured using the biomass balance approach (BMB), to bodyshops various regions globally such as Europe, Middle East and Africa (EMEA) and Asia-Pacific. This innovative portfolio enhances quality and productivity while significantly reducing CO2 emissions, addressing the increasing demand for sustainable solutions in the automotive refinish industry.
Sustainability benefit
Building upon the successful launches of Glasurit® 100 Line and R-M®'s AGILIS basecoat lines in 2020, which feature VOC (volatile organic compounds) values lower than 250 g/l, BASF's biomass refinish coatings with their reduction of CO2 emissions further enhance the scope of environmentally friendly options available to the automotive refinishing market.
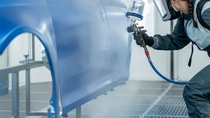
> 7,000 body shops globally relying on biomassed refinish coatings
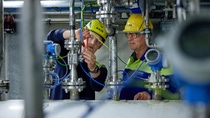
BASF's Chemcycling® initiative focuses on the chemical recycling of materials, transforming waste back into original monomers or valuable products.
This innovative process enables the production of new materials from recycled feedstock, effectively closing the loop in the material lifecycle. For the refinish market, BASF Coatings already offers a range of innovative products based on this specific pillar of the mass balance approach leveraging certified Ccycled® solutions.
Glasurit®’s Eco Balance product range provides a new clearcoat that meets the highest standards of modern bodyshops and is manufactured using BASF’s advanced Ccycled® technology. This innovative clearcoat utilizes raw materials sourced from recycled waste tires to replace fossil feedstocks, while simultaneously offering technical advantages such as reduced energy consumption and enhanced throughput.
Sustainability benefit
Enabling bodyshops to cut drying time in half (ready in 20 minutes at 40 ºC and 10 minutes at 60 ºC), delivering energy and cost advantages. Contributes to a circular economy with up to 40 % less CO2 per kg of product.
* Carbon footprint data is based on assumptions and approximations valid at the time of data collection. For more information, please visit: ecobalance.glasurit.com
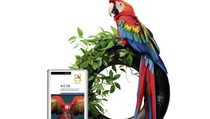