Coatings
Circular Economy
A circular economy can revolutionize our industry landscape by reforming supply chain approaches. Instead of the traditional linear model, there will be a transition towards rethinking, reusing, refurbishing, repurposing, and recycling materials. The benefits include conserving natural resources, reducing the risk of shortages, and ensuring continued access to raw material sources.This reduces CO2 but while also reducing costs in the long run. In essence, a circular economy means decoupling growth from resource consumption. At BASF Coatings, we strive to become an enabler for a circular economy by prolonging the usage of resources, minimizing waste, and creating value by incorporating renewable resources into our processes.
Overall, coatings and surface treatments play a pivotal role in the circular economy by empowering materials with protection and decoration. This not only preserves their value but also holds the potential to enable the closing of the loops.
Surface treatments and coatings protect materials from corrosion, ultraviolet (UV) radiation, and wear and tear, maintaining their aesthetics for a longer period. This fundamental principle significantly contributes to the circular economy by extending the lifespan of products, such as vehicles and airplanes, reducing the need for new production. Designing for durability is therefore critical to minimize the environmental footprint. This goal is continually pursued through the development of innovative products derived from safe and sustainable raw materials.
However, we do not rest on these benefits. Instead, we actively seek opportunities to become an enabler for the circular economy. This involves adopting a genuine life cycle perspective and understanding our influence on the value chain of our products, as well as those treated or coated with our materials. The so-called Butterfly Diagram provides a valuable overview, showcasing both the technical and biological cycles.
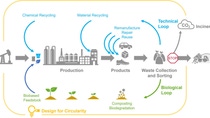
We can contribute to closing the biological loop through the careful selection of our raw materials. In this process, we evaluate the potential of different approaches.
For example, we assess the applicability of bio-based raw materials in our products or use the mass balance method, which incorporates biomass (Biomass Balance) or recycled materials (ChemCycling®) in preliminary products. These materials are subsequently allocated to our products. Through this approach, we can effectively reduce greenhouse gas emissions by using circular feedstocks.
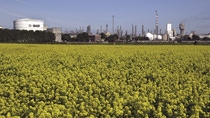
Let's consider the technical loop of our products along the value chain, there are various starting points to promote the circular economy.
We actively drive recycling processes in our operations, minimizing waste and resource consumption. For example, we have developed and implemented a MEK recycling processes at our plants in Shanghai and Muenster. By clever combining distillation and other phase separation steps at different temperatures and pressures, MEK can be purified from a complex waste mixture at high yields – able to reuse it in the production process, instead of using fresh MEK each time. This significantly reduces waste and resource consumption.
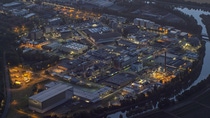
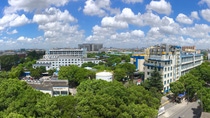.jpg)
Recycled packaging in our Decorative Paints Business
We see great potential in rethinking not just our products, but also the auxiliary materials involved in our production process. Take for example our Decorative Paint Business in Brazil, where we use recycled packaging to reduce waste. This seemingly small change has a significant positive impact on our environmental footprint. It's these opportunities, often overlooked, that can drive sustainability and innovation in our operations. Simple shifts including the use of sustainable alternatives for these materials can reduce waste and CO2 emissions, enhance the quality of our products and reinforce our commitment to our customers and our planet.
It's crucial to not only focus on our own processes and value chains but also those of the substrates, to support our customers optimally.
Coatings, for example, not only enhance a product’s lifetime but can be redesigned or repaired to extend their service time. However, the end-of-life material mix in complex systems often hinders recycling. To overcome this, we are researching and working with partners to develop recycling solutions, including innovative ways to separate coatings from substrates. Our findings are driving innovation and further fostering a circular economy, where the value of materials is kept in the cycle for as long as possible. This approach is transforming design processes, leading to products that are easier to deconstruct and reuse, which reduces demand for new parts and virgin materials. This shift is accompanied by new business models, such as renting out vehicles, which encourages manufacturers to use higher-value materials and maintain products for longer.
MEK Recycling
At MEK Recycling/Reuse, we actively drive recycling processes to minimize waste and resource consumption. Our plants in Shanghai and Muenster feature innovative MEK recycling processes.
MEK (Methyl Ethyl Ketone) is a solvent used in the production of waterborne paints. It plays a crucial role in the production of waterborne polyurethane dispersions. Without MEK, it would be difficult to achieve the desired product properties. To prioritize sustainability and reduce our environmental impact, we have developed a recycling unit for MEK. This process allows us to separate the MEK solvent, water, and contaminants from the polyurethane dispersion. The result is two products: a stable and solvent-free polyurethane dispersion for use in waterborne basecoats and a distillate containing the separated MEK, water, and contaminants. Rather than disposing of the MEK distillate or using as a substitute fuel for natural gas, we reuse it in the production process, significantly reducing waste. By recycling and reusing MEK, we not only minimize waste but also reduce resource consumption. This sustainable approach has a positive impact on the carbon footprint of our waterborne basecoats, making them more environmentally friendly. We are proud to lead the way in the industry with our MEK recycling initiative. Our commitment to resource efficiency drives us to continuously find new ways to reduce waste and optimize our processes.
Material Perspective
Looking at the technical loop of substrates, we recognize that coatings enhance a product's lifetime by protecting it against a multitude of external influences. Moreover, these coatings can be repaired or used for product redesign, thereby prolonging its potential service time. However, the challenge arises when the product reaches the end of its life cycle. The material mix in complex systems like cars often hinders the product from entering a second cycle, leading to burning or dumping in many cases.
To tackle this, we actively explore alternative processes and collaborate with partners throughout the value chain. Our research is heavily focused on reuse and recycling options, the findings of which drive innovation and help create solutions that close the loop.
One such solution involves recycling the combined material through a cradle-to-cradle process. We also offer product solutions like cleaners for all types of plastic, which further support the economic and ecological benefits of recycling. Coatings designed for recycling enable a circular economy, keeping the coated material's value in the cycle for as long as possible.
We also foster circularity by providing solutions to remove residues, labels, and adhesives from bottle material, which is a crucial step in plastics and PET recycling. Special cleaning agents and defoamers ensure increased productivity and safety of recycling processes.
A significant factor contributing to the loss of valuable materials is their integration within complex multi-material parts, making them difficult to access. The energy and time required for deconstruction often outweigh the potential benefits. However, with the rising costs of virgin materials and growing pressure to achieve higher recycling rates, there's an increasing incentive to design products that allow easy access to pure material waste streams. This design shift could profoundly impact intricate systems like cars, leading to substantial transformation. At the end of a car's life cycle, many parts are still functional and can be reused. Easy deconstruction is key to repair or replace unacceptable parts, reducing the demand for new parts and virgin materials while saving energy.
This shift towards resource-efficient models is accompanied by new business models, such as renting out vehicles. By retaining ownership, manufacturers have a vested interest in keeping products running for as long as possible with minimal effort and additional resources. This also influences raw material selection; knowing that products will return allows for the use of higher-value materials that extend the product's life even further.